A problem for a plumber.
When it's the supply pipework causing a leak, it's time to call in a plumber!
Today, I visited a customer where it appeared that the dishwasher was leaking.
Clean water was appearing beside a built-in dishwasher on an 'island' in a kitchen.
This was a bespoke kitchen, with hand-built units. I couldn't pull out the dishwasher to thoroughly check out the cause due to the way that the fitters had installed it. It was fitted in such a way that the dishwasher could not be removed, as a wooden strut had been fitted across the dishwasher without any visible way of removing it.
I was able to get to the back of the dishwasher through the opposite side of the island which had a cupboard under the island sink. It quickly became clear that the fault was not with the appliance itself, but with the pipework supplying it.
The dishwasher supply pipework has a fitting that has a compression joint. This had a small bead of water above it which was causing a tiny leak.
I'm not a plumber, but I got my grips and a spanner and tried to tighten this up but the nut didn't move at all. That's as far as I was willing to go with it as I had visions of the fitting splitting at full mains water pressure with no way of turning off the supply. I certainly didn't want to risk this so I had to advise the customer that they would need to get a plumber in to rectify the fault.
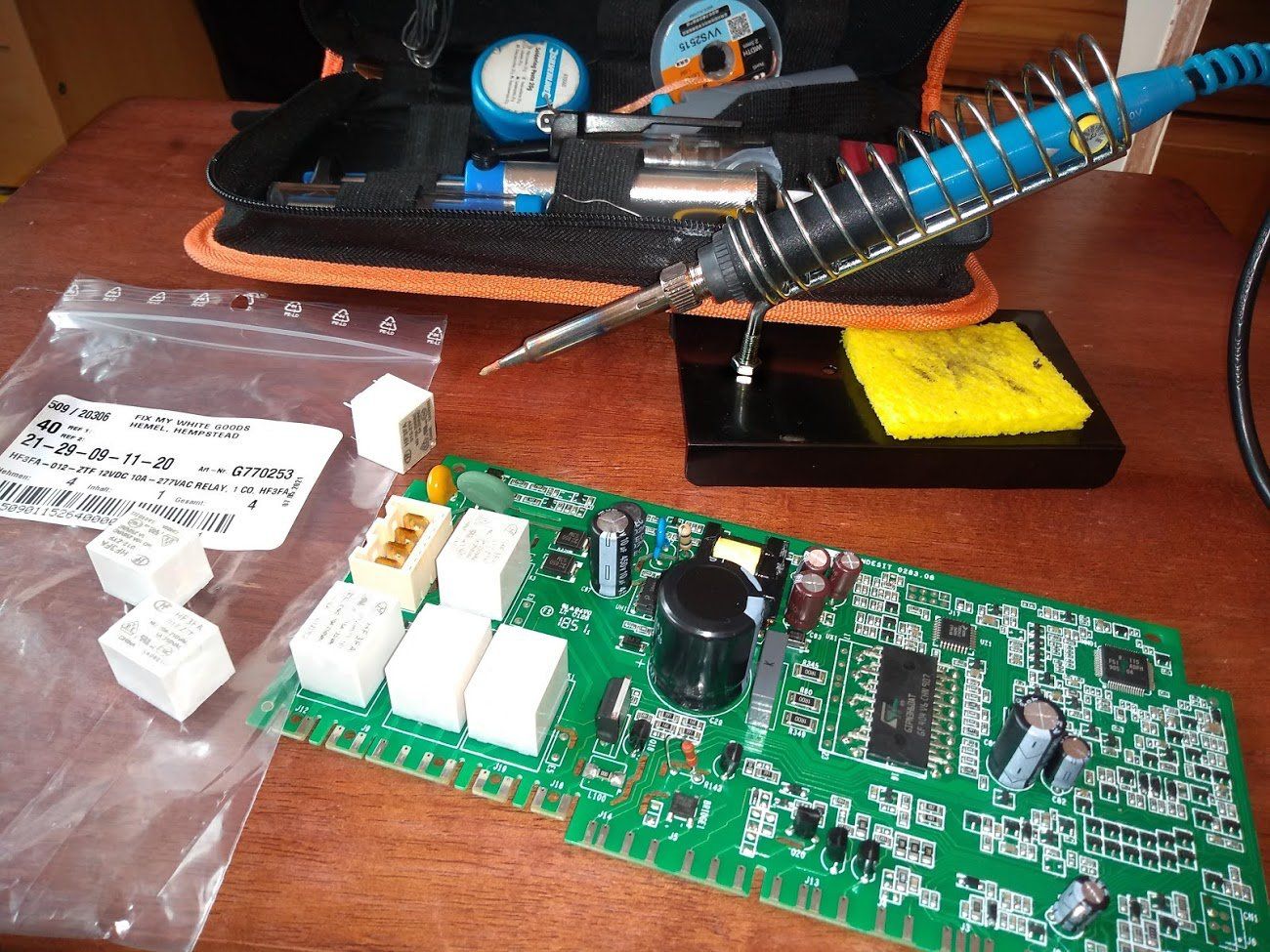
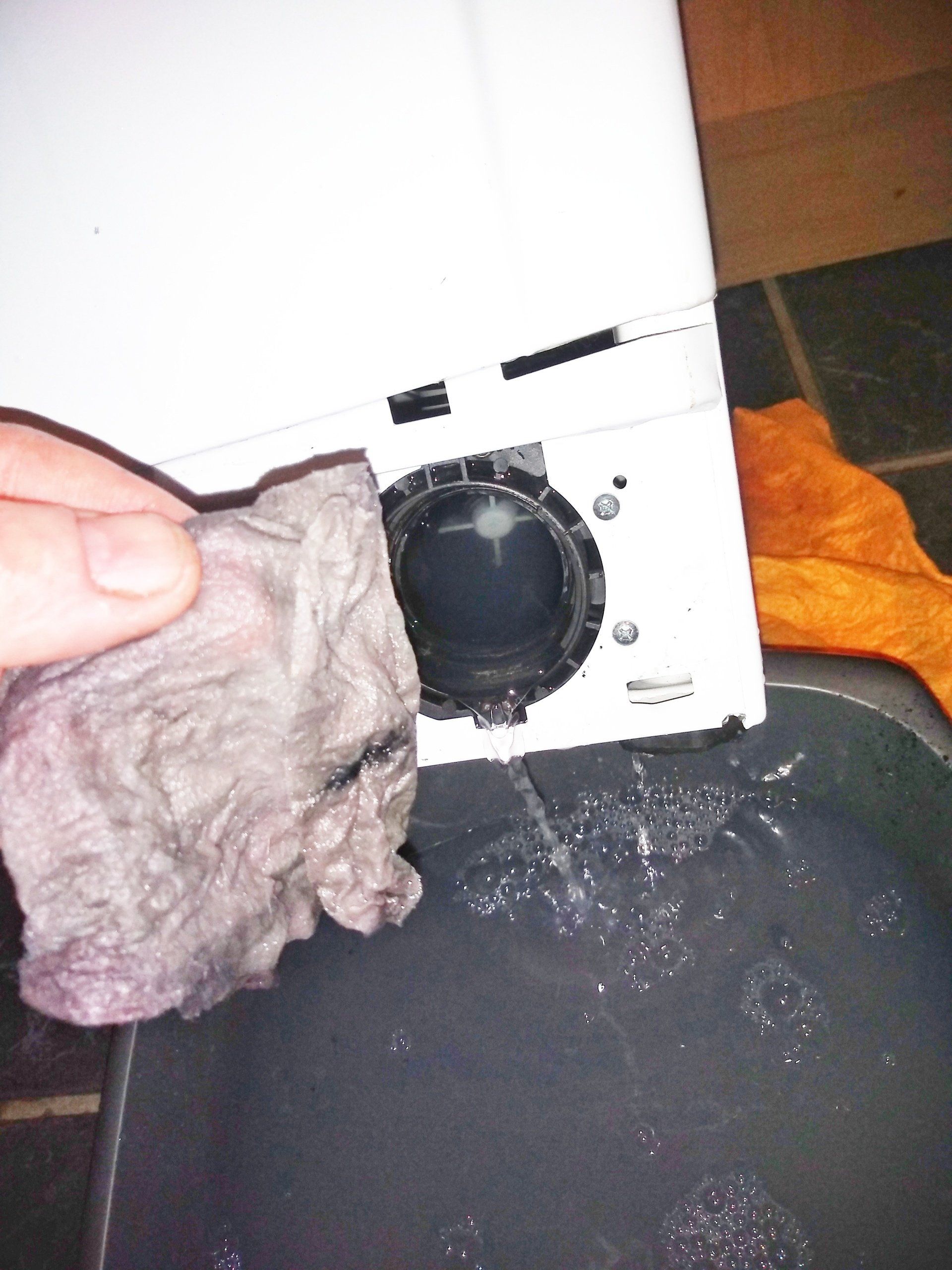
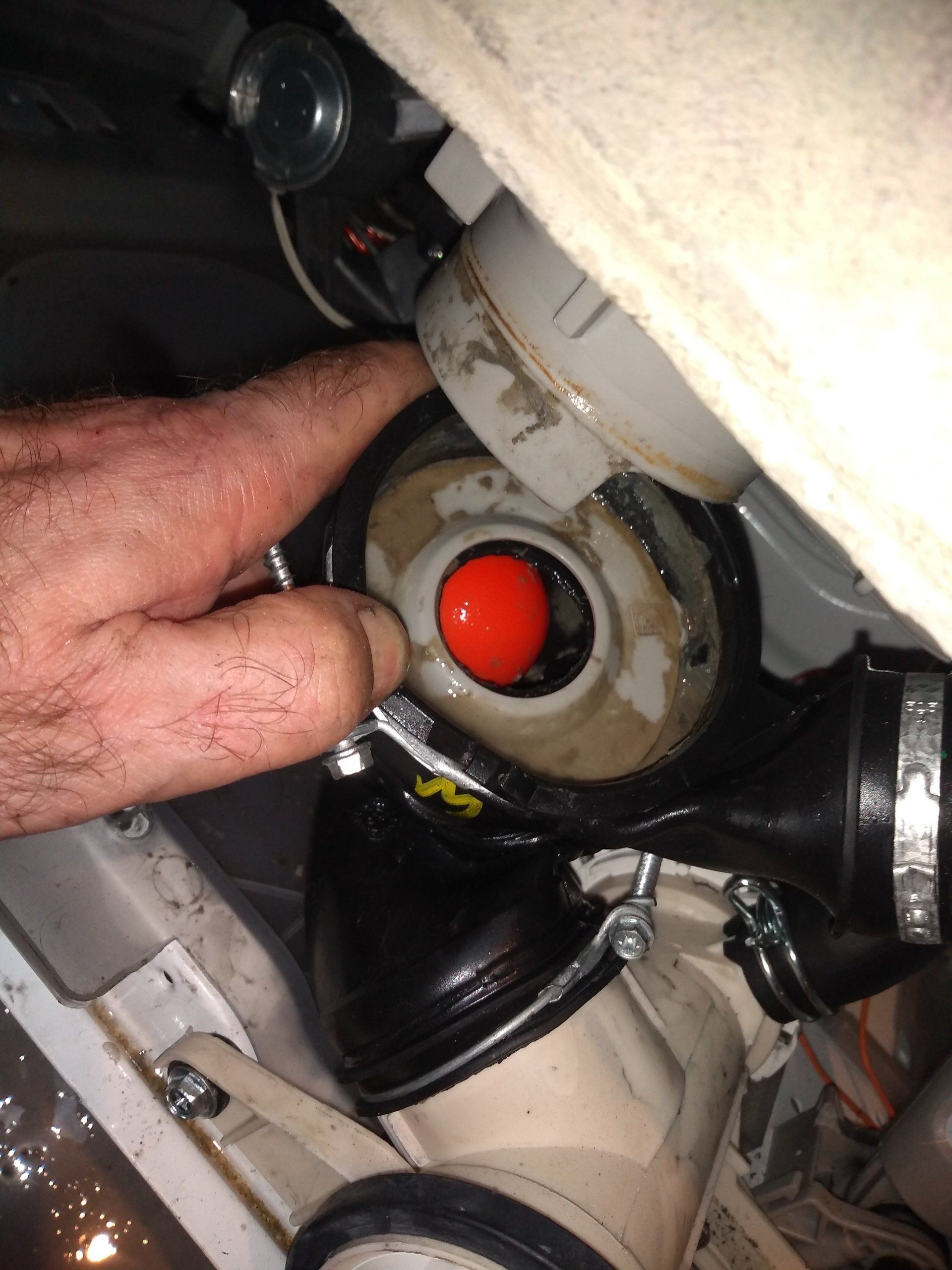
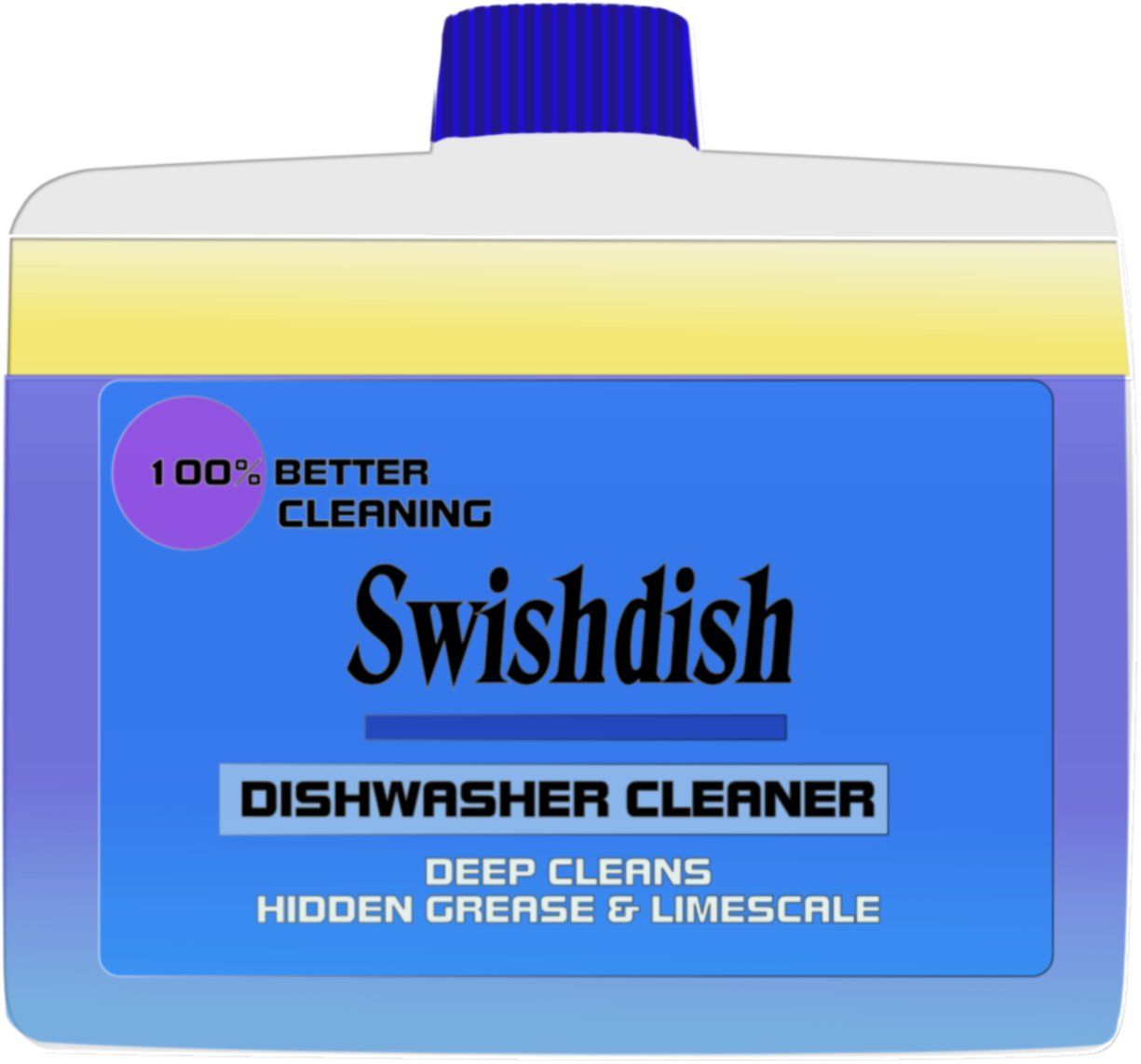
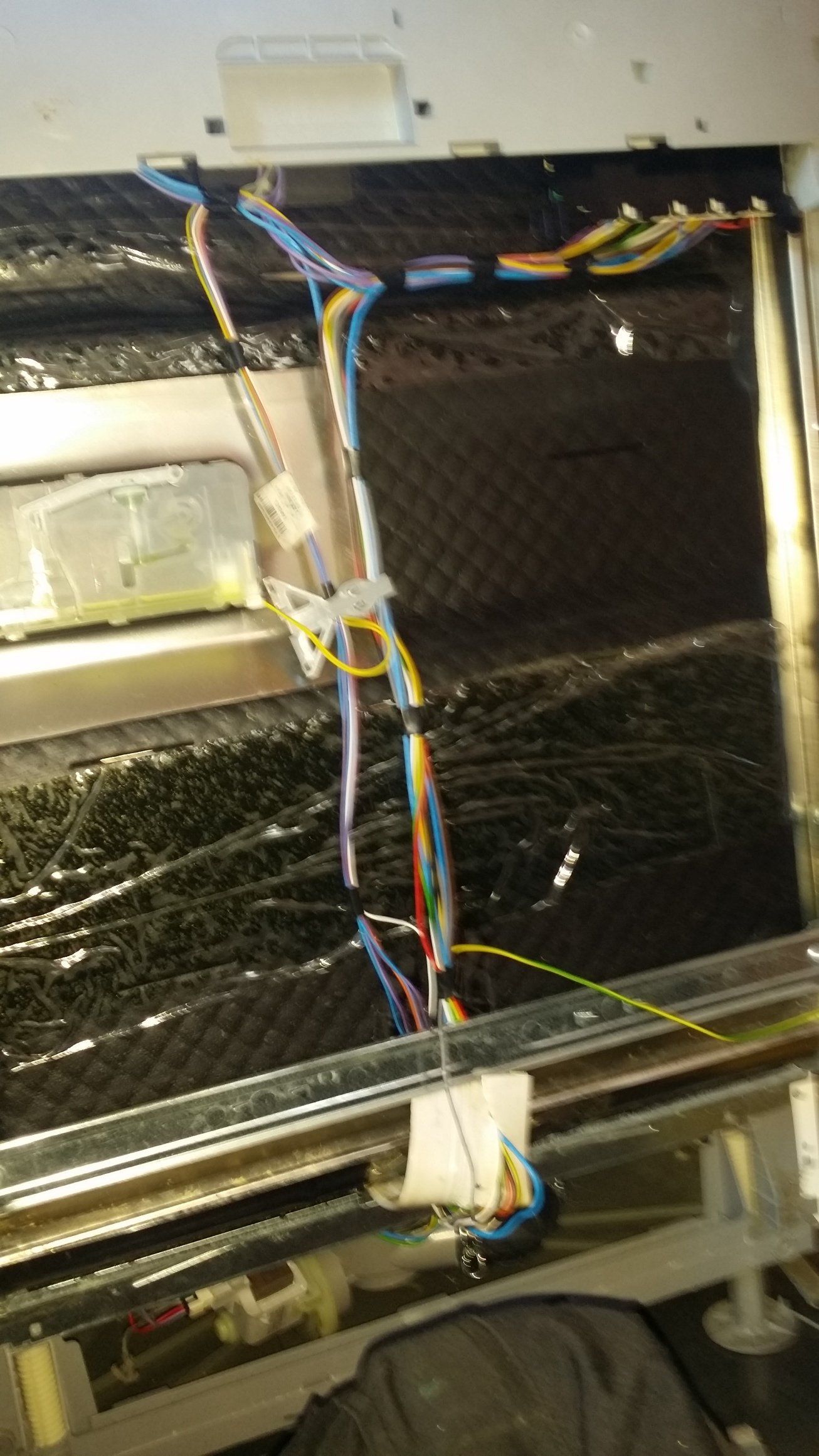